Making Face Masks
As soon as it become clear that, at least for awhile, we all need to make our own face masks, Nick and I have been thinking about what tools we have that could be useful. I couldn’t figure out any way to use our full-frame quilting machine in a useful way. All the designs require either pleating, or non-flat shapes, neither of which it can do. Nick started making pleated-style masks using Hank, our sail-making machine.
I wasted time on a few dead ends before my girlfriend, ignoring me, started making what I call the “bra-cup” style for which various people have posted patterns. I now call it the Maribel-style. This mask requires—for a three-layer mask—six pieces of fabric cut to a complicated curvy shape. AHA, for that we have the tool!
Here’s a video of our GU Eagle 1390 laser cutter cutting out 320 half-mask pieces simultaneously out of 8 layers of fabric.
I’ve had this machine for years, and never once used it to cut fabric (we make acrylic models, not clothes). But actually the mass-production textile industry is a heavy user of laser cutters. I’m told the one of the largest markets for the GU Eagle brand I use is shoe manufacturers, who use it to cut out the soles.
Cotton fabric cuts beautifully, with just a bit of darkening on the cut edge. This is no problem because you always fold over and hide such edges anyway: you can’t leave a raw edge exposed or it will unravel when the item is washed. Speaking of fabric, another asset we have in the production of face masks is lots and lots of scraps of fabric. (The piece in the video might not look like a scrap, but in the context of a full-frame quilting machine, anything less than about 2 yards of 108” wide fabric is a scrap. That’s about the size of the piece that made these 320 segments.)
For the pretty outer shell we’re using various patterns we had lying around, or that someone liked. You can create either a positive or negative image of the laser’s work by removing either the waste or the good bits first…. I figured out that if I cut the fabric good-sides-in, the two halves of a shell very slightly stick to each other, enough that if you’re careful picking them up, you can get them to the sewing machine and sew the seam without having to align and pin it, which saves a good bit of time.
That’s about it for modern technology. After the cutting, the sewing is old-school work with an ordinary domestic sewing machine.
The one on the right is my mom’s old Singer 5127 from the 1980’s. It is, of course, far superior to the new one on the left: it’s comparable in construction to our modern commercial machines, except it does have a plastic pattern cog and one plastic curved rack gear. (Singer literally invented planned obsolescence, so their consumer machines are currently textbook examples of things designed to break.) I had to soak one main bearing in oil overnight to get it loosened up after years of sitting (a suggestion from my friend Chris Anderson, who knows about these things). And I had to reset the hook timing and needle gap: not sure how those got out of whack.
One of the painful steps is ironing the vertical seam to flatten it out for when the layers are joined along the top and bottom. I laser-cut and filed a wooden “saddle” made from five layers of 1/4” plywood, using the cutting pattern as a starting point. This makes the ironing go a lot faster.
My job is cutting the fabric, sewing this vertical seam, and ironing it. Here’s a stack of these parts before I hand them off to my girlfriend.
I also have a side-job twisting wire to make our nose wires. I find that most masks have a nose wire that is way too flimsy. It straightens out as you wear it, and then my glasses fog up, proving there is no good seal. We have settled on a tightly twisted pair of 20 gauge bell wire, mainly because that’s what I had, and it feels better than 14 gauge solid copper, which is the other thing I had. It’s good stuff, and should stand up to many cycles of bending.
We’re chugging along making these for friends and family and friends of family and family of friends of family and people at the restaurant where the girlfriend works. Since everyone really needs several masks (so they can be washed regularly and warn every time you go out in public) the number required is really quite large.
UPDATE: Having satisfied domestic requirements, and due to overwhelming local neighborhood demand, we have now started selling the masks, as well as kits of materials for making your own.
Now, on the subject of filters, there are different schools of thought. Our masks include a pocket between the two inner layers of fabric, into which you can insert a specially cut sheet of filter material. We are including several sheets of what I’ve been using, which are cut from 6” deep pleated furnace filters, supposedly MERV 13 but probably not (they were too cheap).
If you take the filter seriously, it needs to be changed every day, and that gets expensive. On the other hand, it’s unclear if having a filter actually makes any difference. Without the filter you still have three layers of fabric, two of which are fairly tight 100 thread count quilting cloth, and one of which is variable, between 60 and 120 thread count depending on the design. All are 100% cotton not counting ink and sparkles.
It’s not clear that laser cutting is an effective way of cutting out the filters, because they come out smelling…smokey. Well, they are filters, their job is to trap smoke, so this should come as no surprise. And you can’t wash them like you can fabric. After a few days they don’t smell nearly as smokey, so maybe it’s going to work this way, otherwise we have to hand-cut, and that’s no good. I’m considering the option of making a punch and die set, but I don’t really look forward to that job.
Once our larger quantities of elastic and cord locks come in, hopefully in a few days, I’m thinking about making available kits of all the parts (six pieces of laser-cut fabric, a length of elastic, a cord lock, and a starter pack of filters) for people who want to sew their own. If there is interest. In the mean time, here’s a gallery of the ones we have made so far.
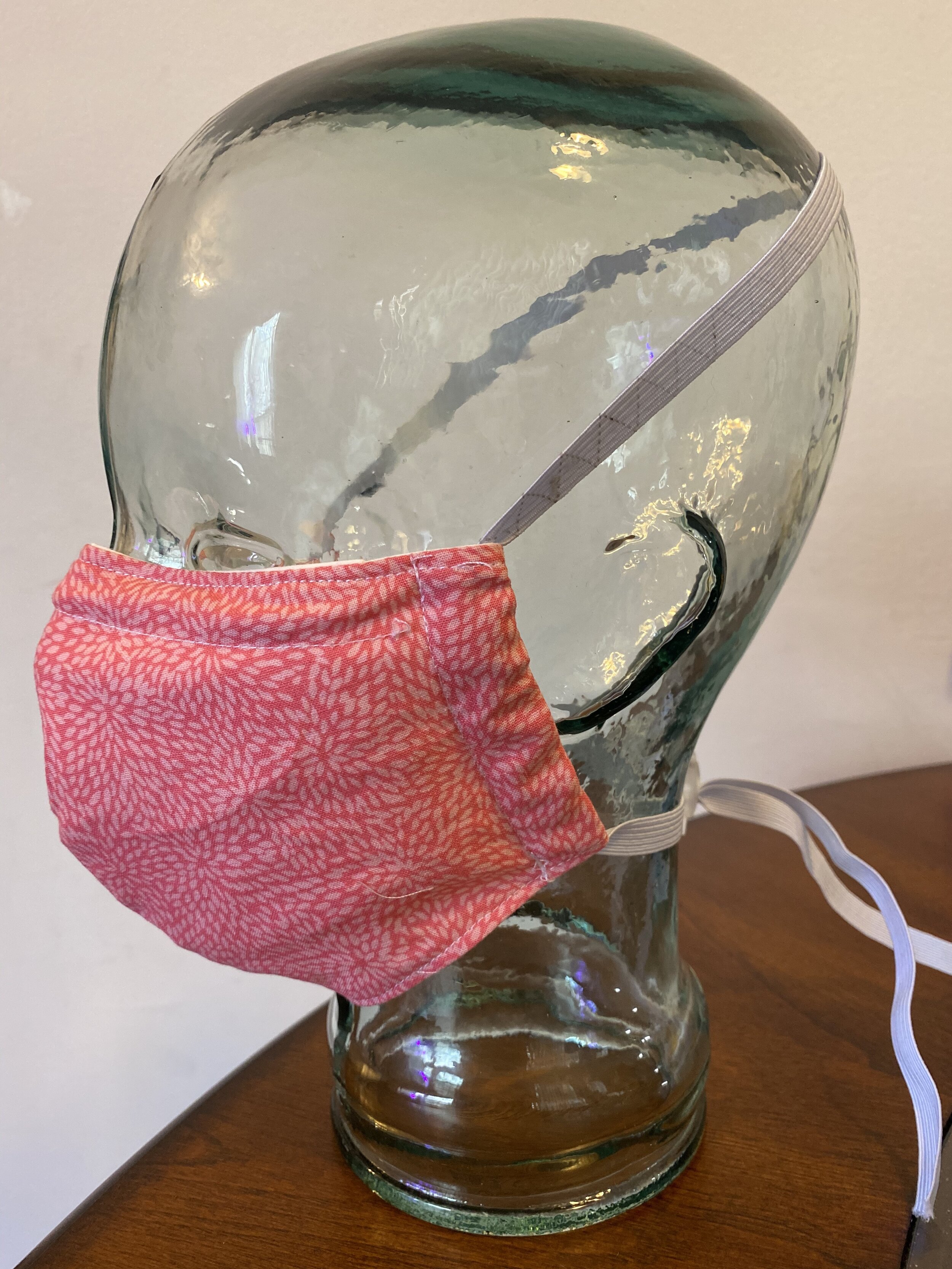
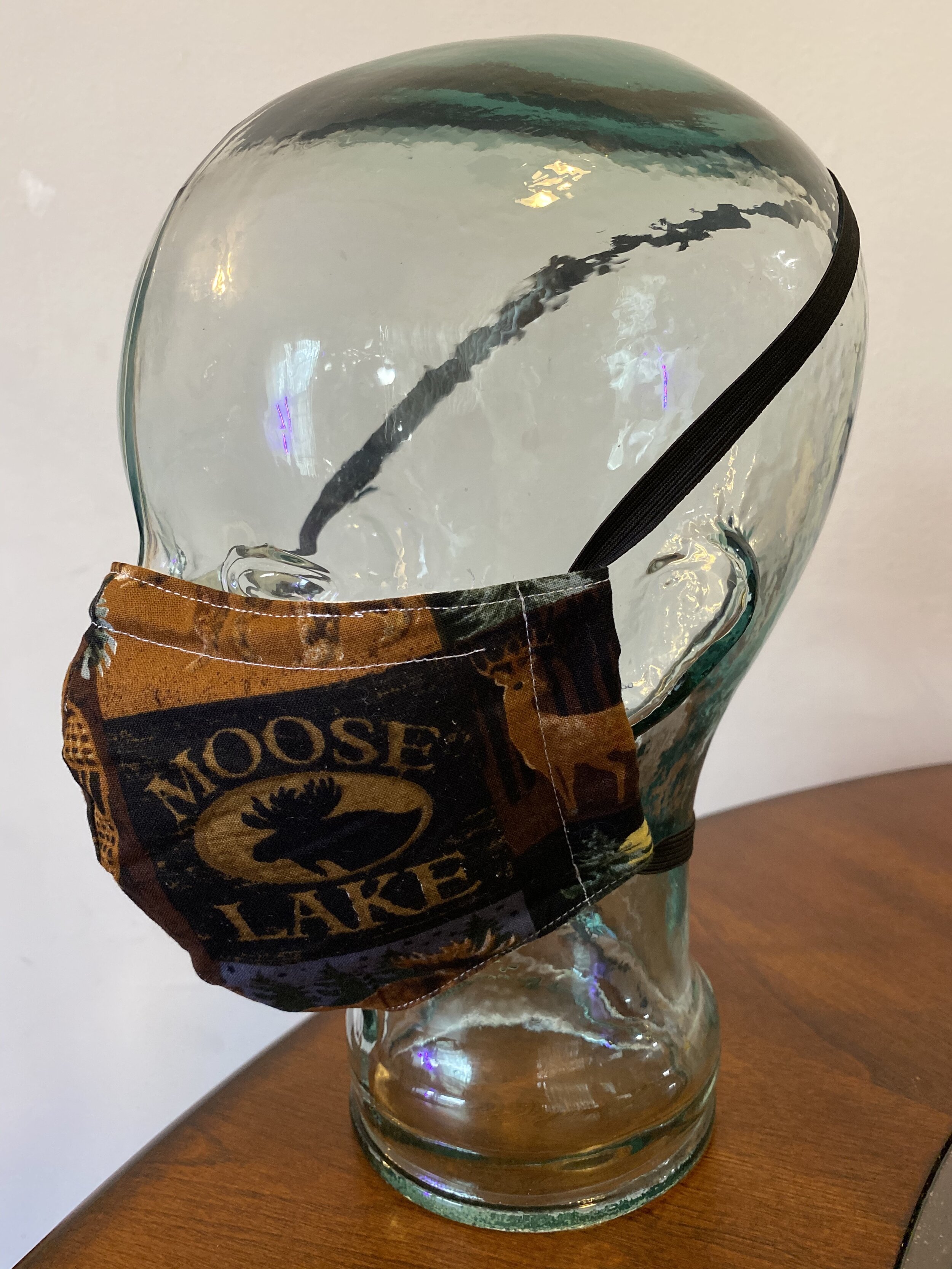
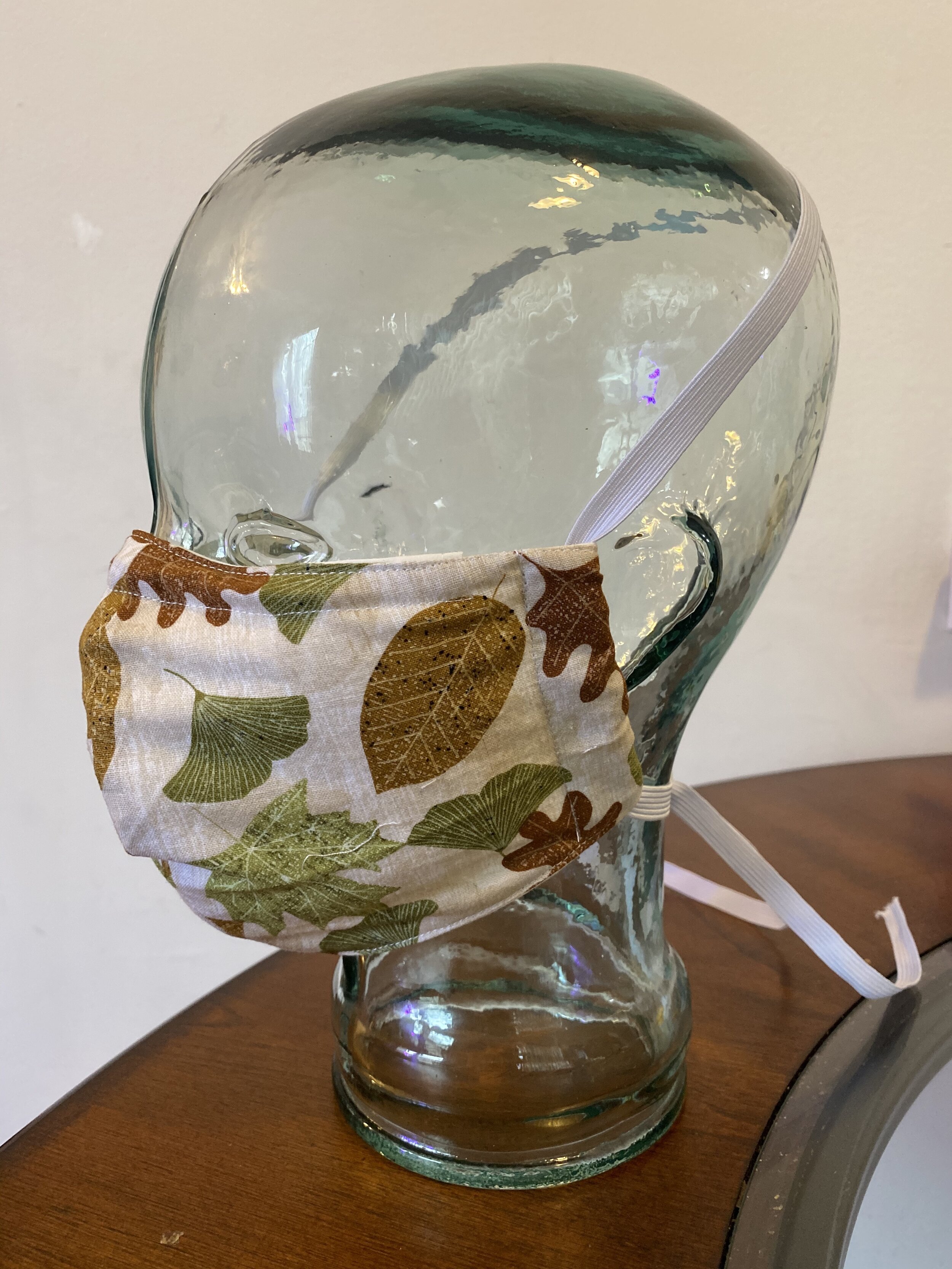
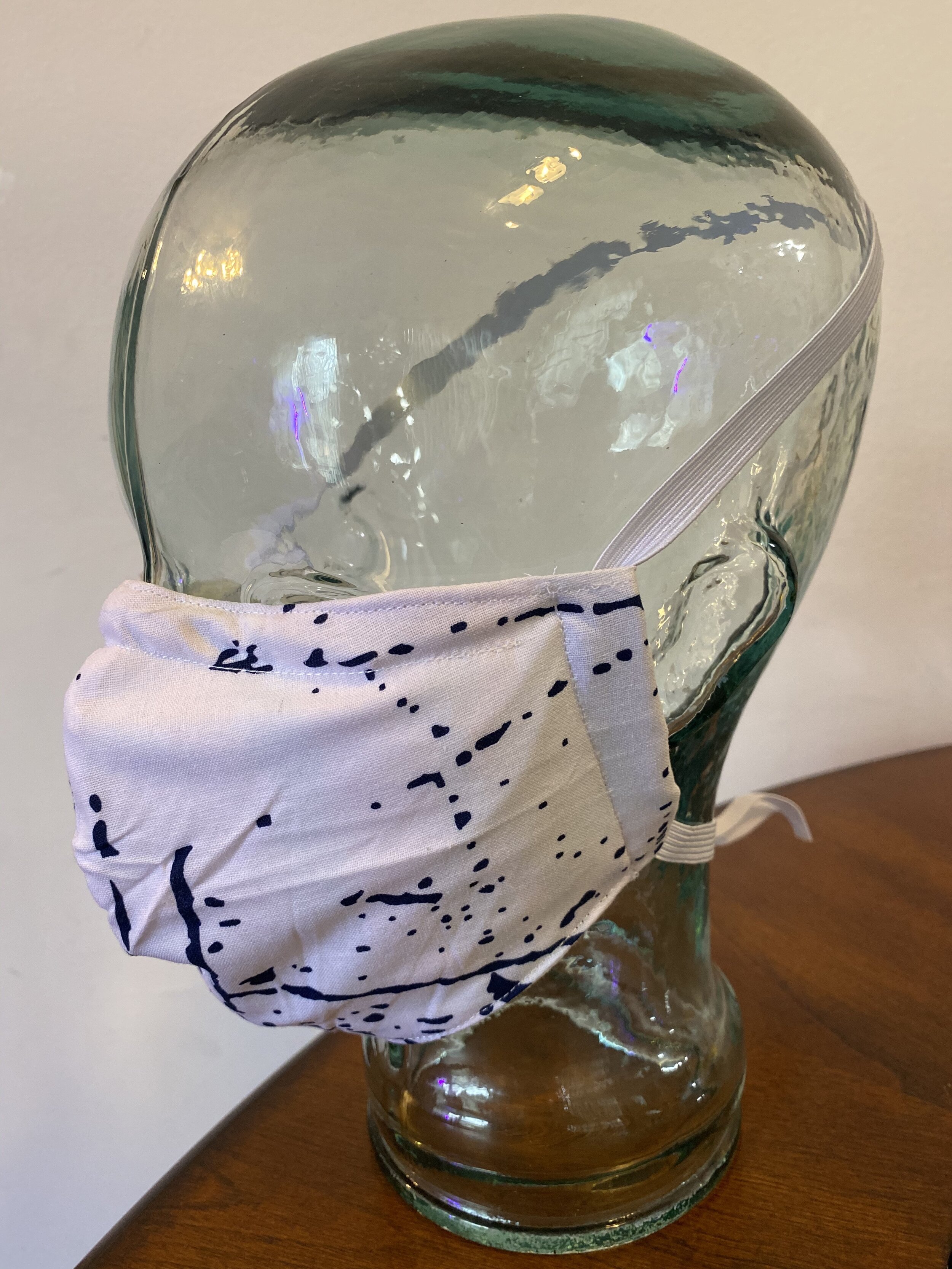
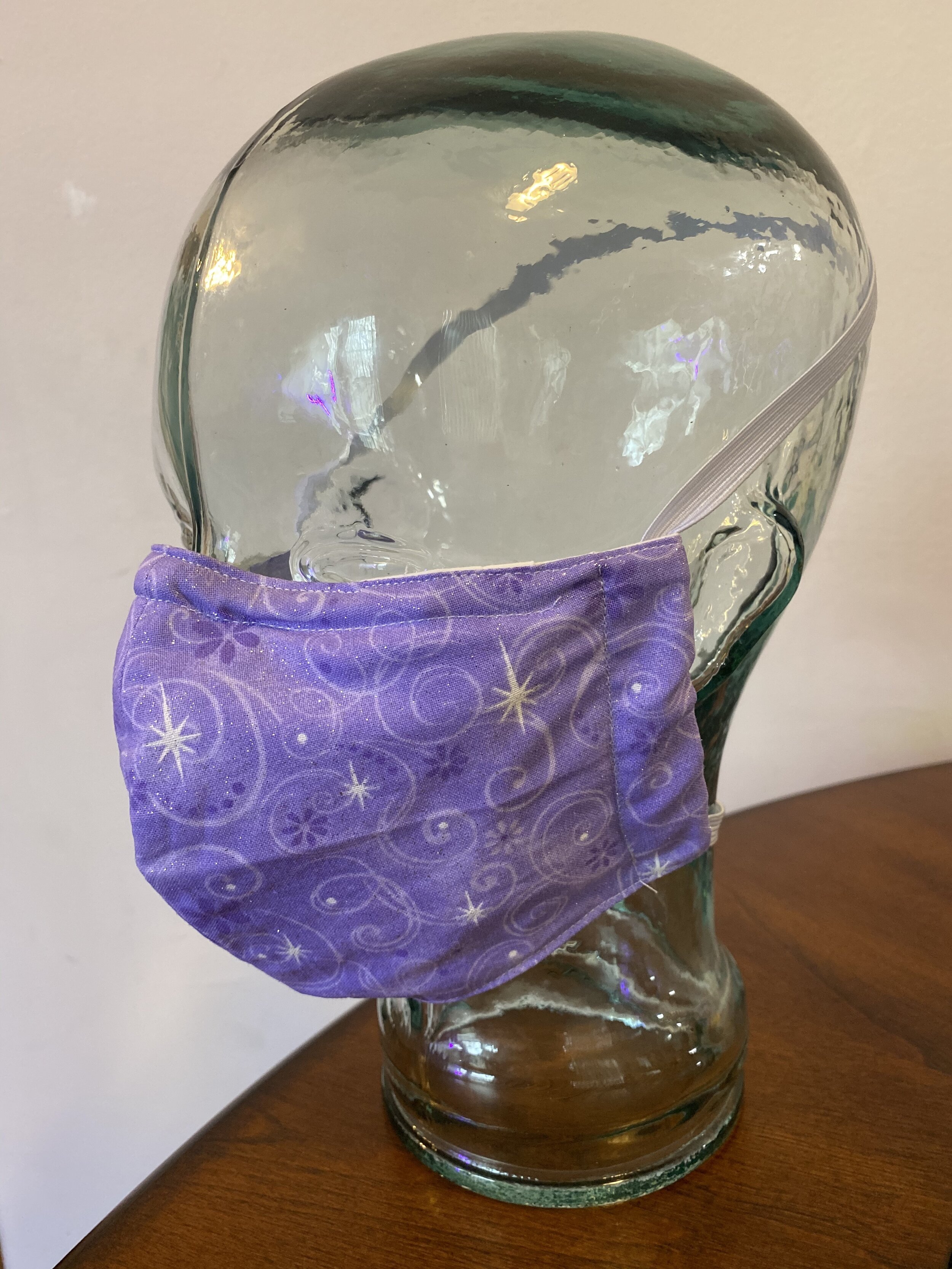
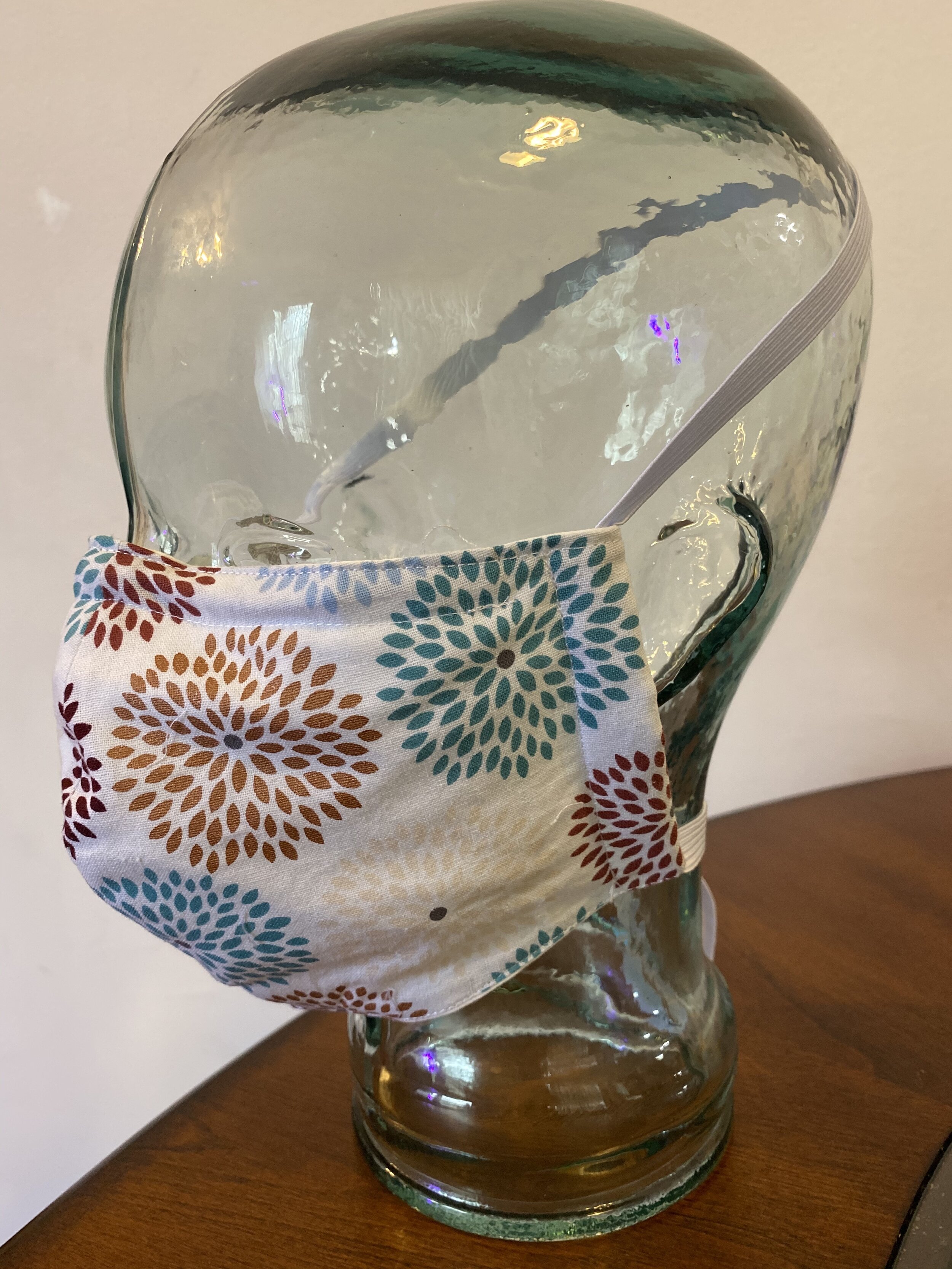
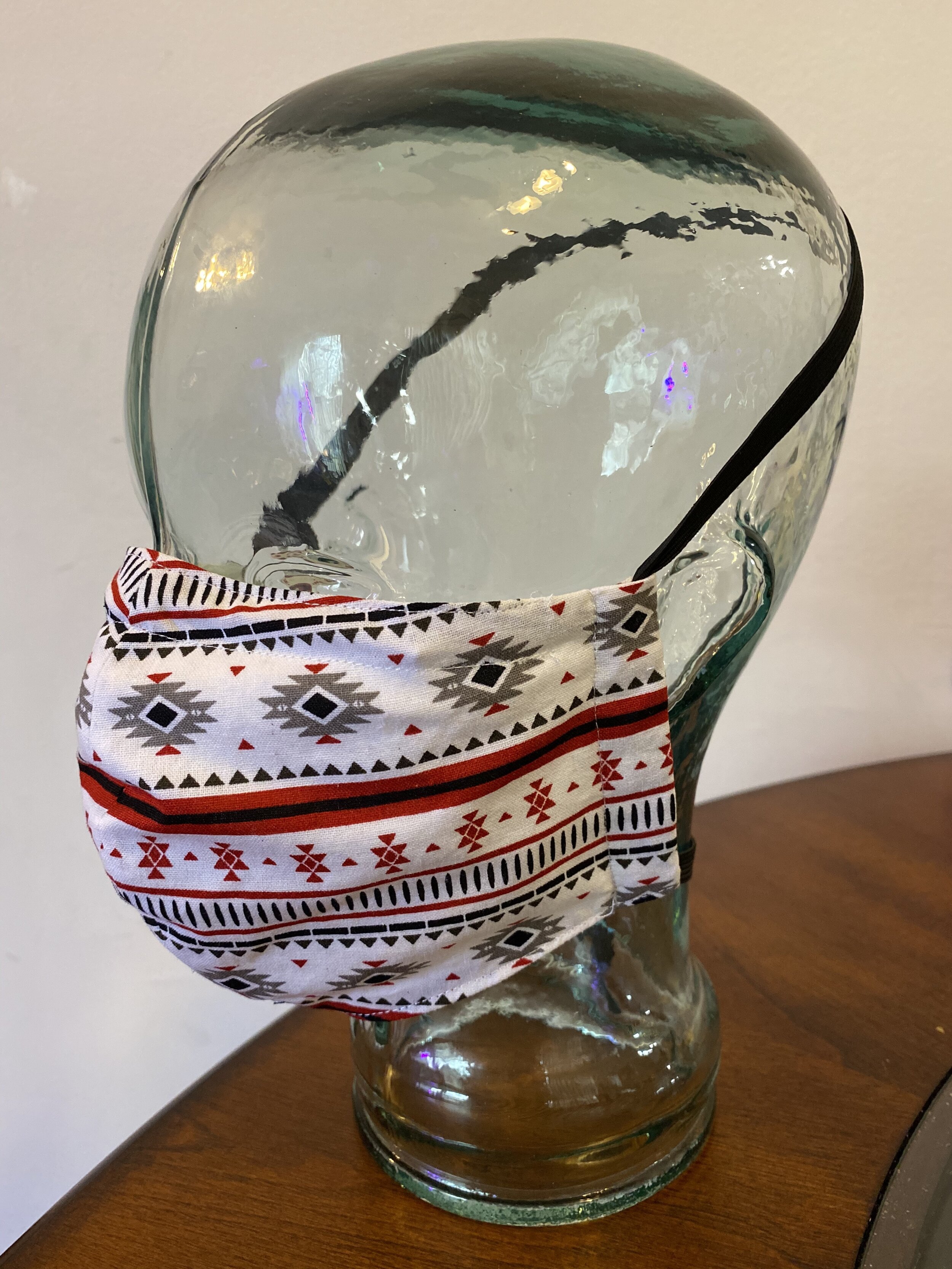
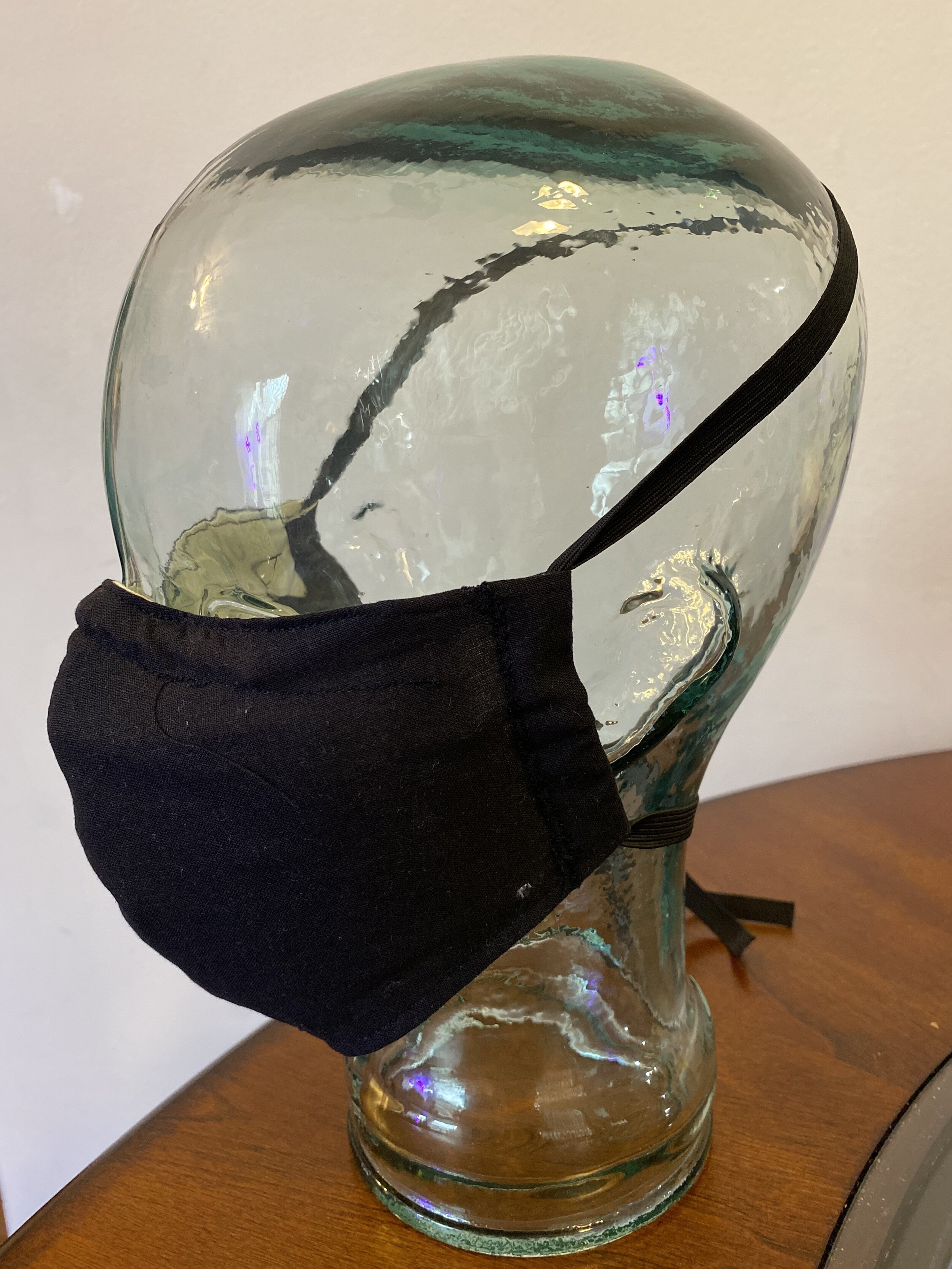
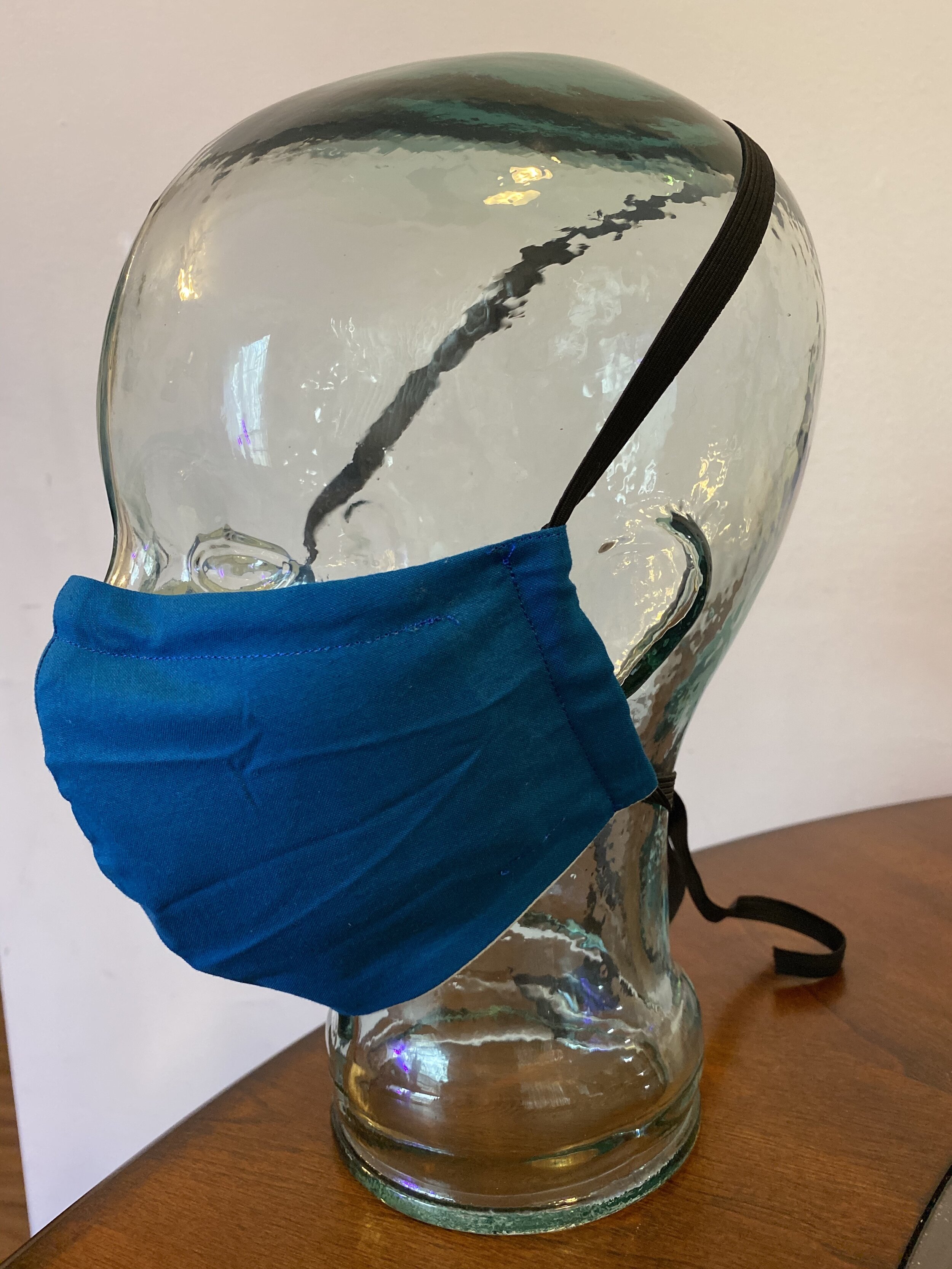
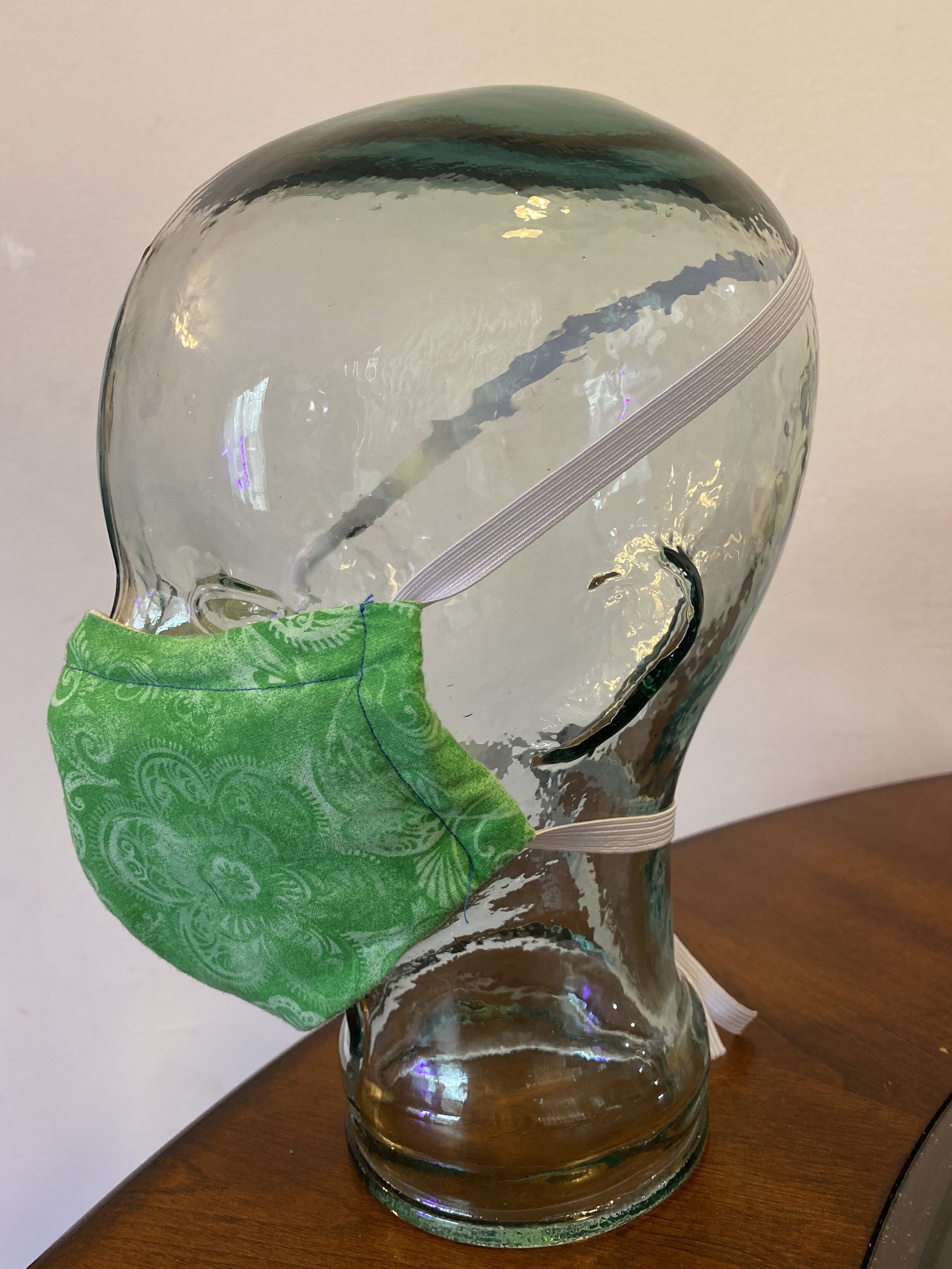
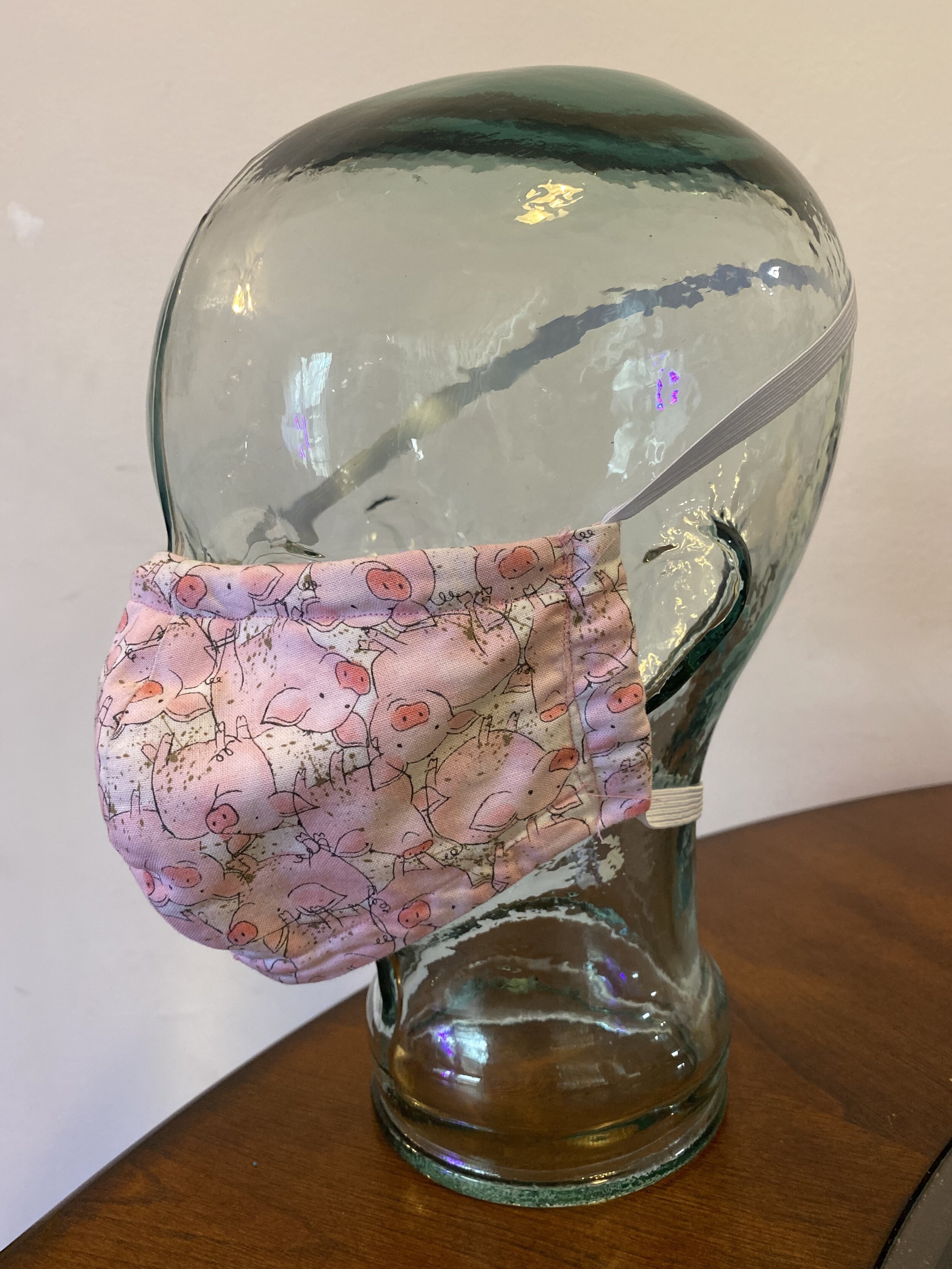
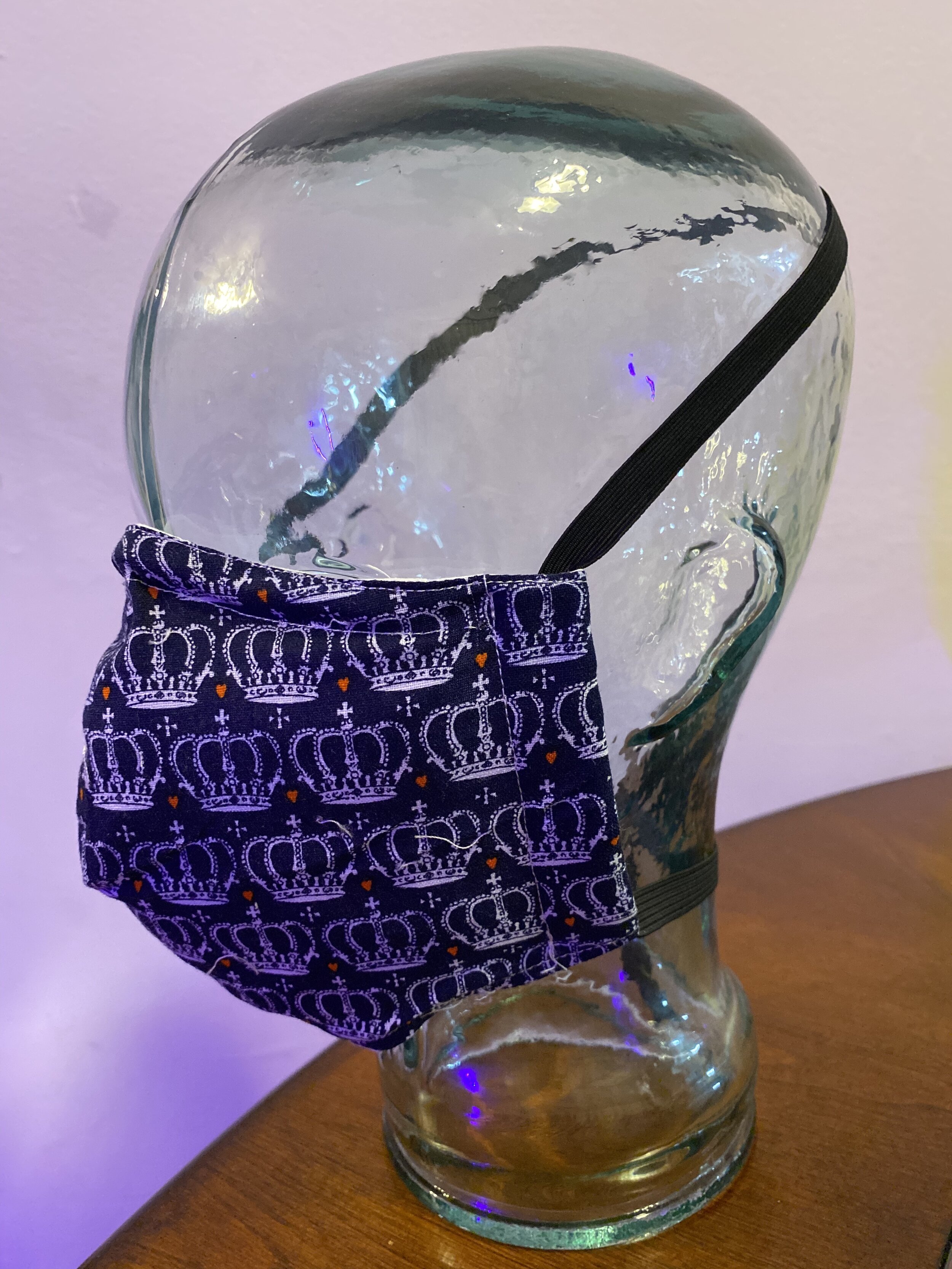
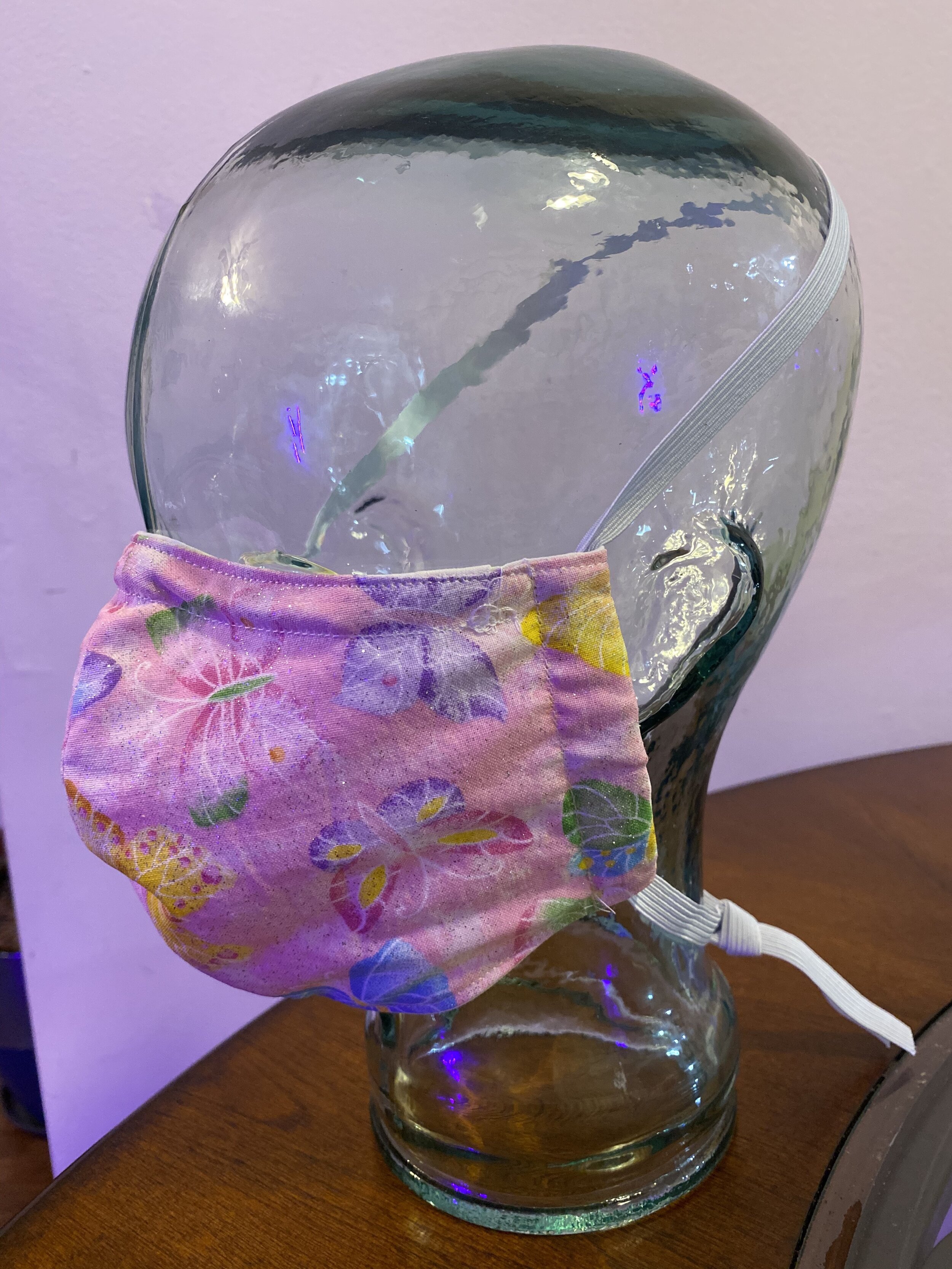
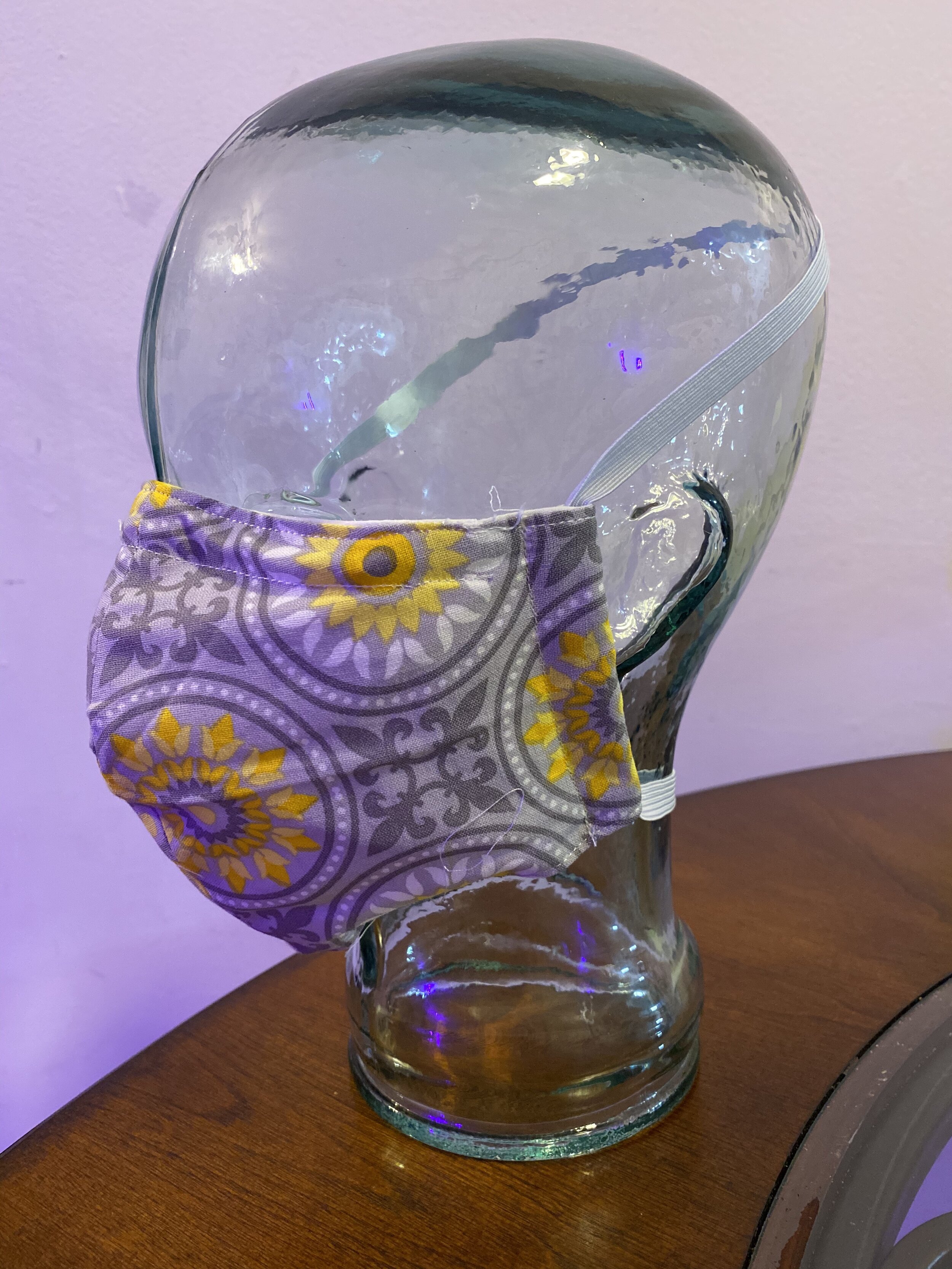
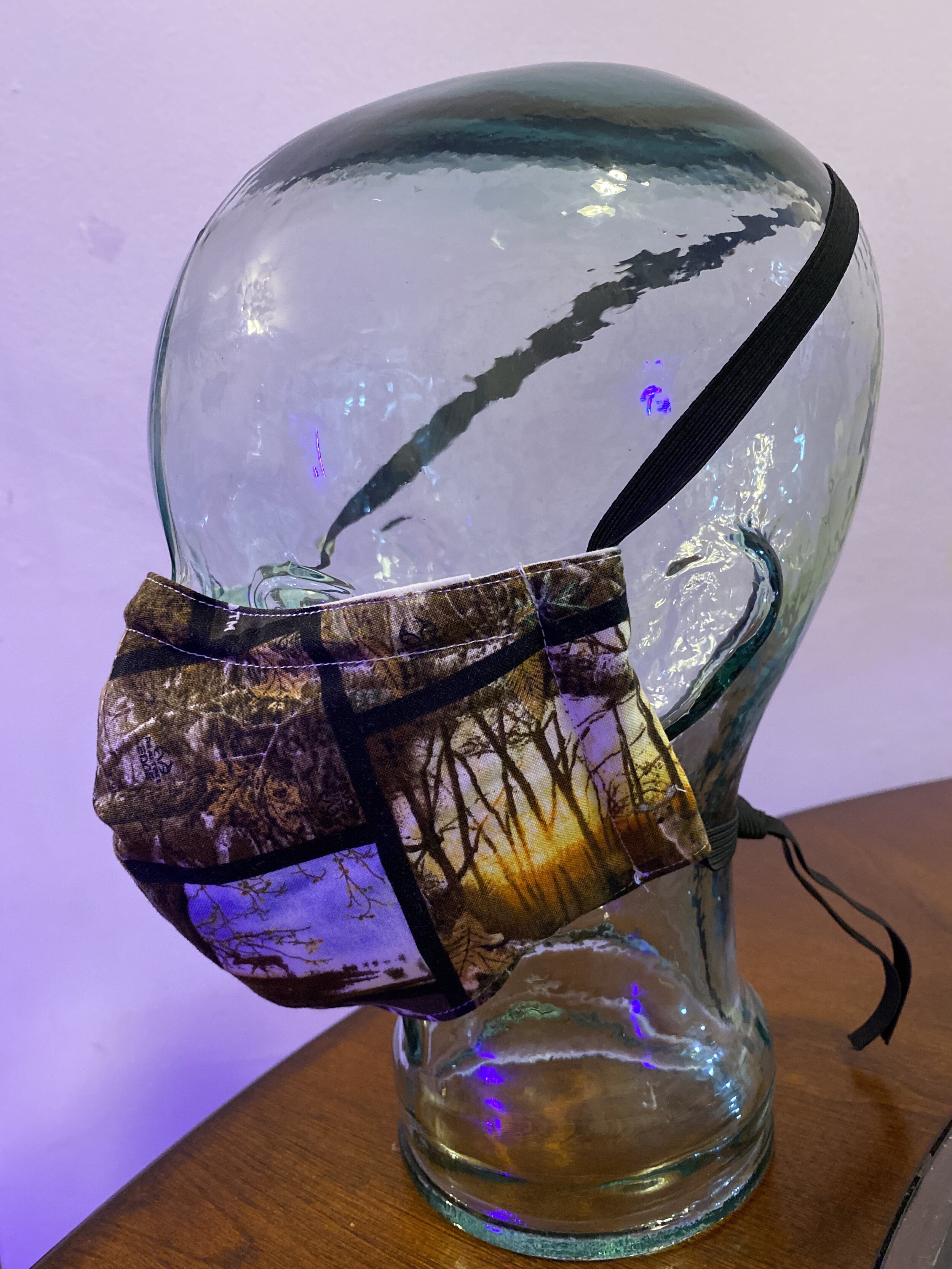
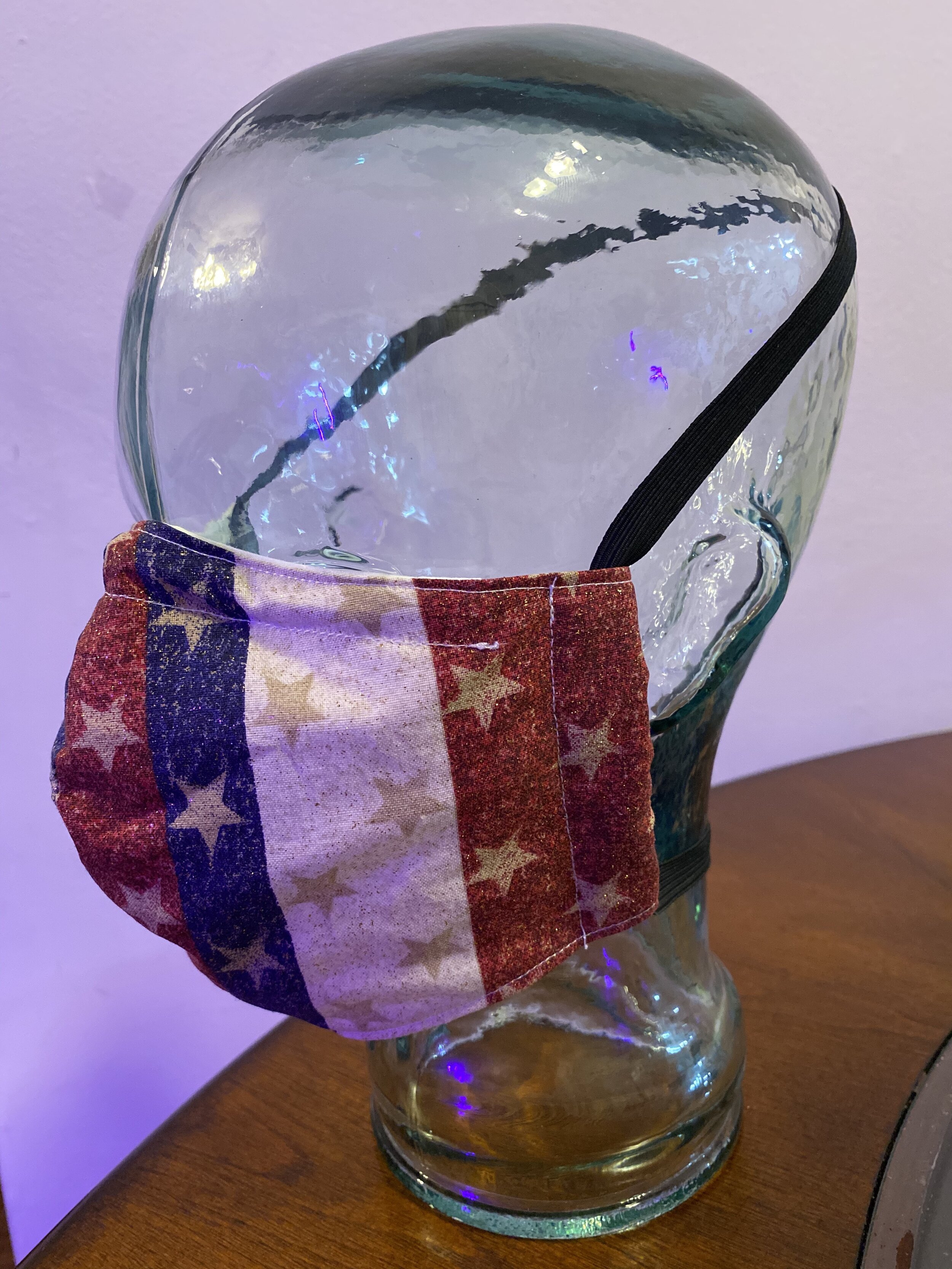
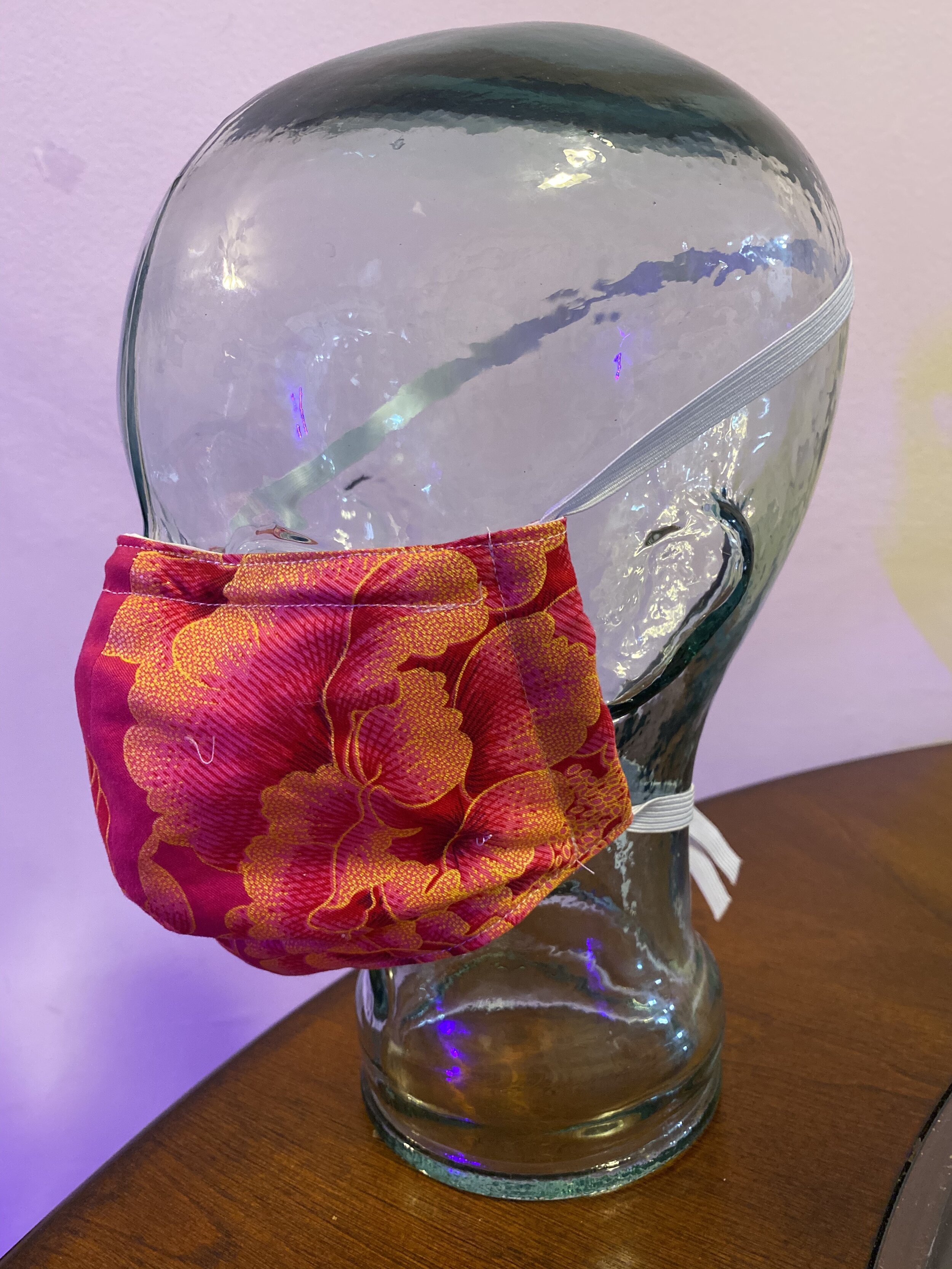